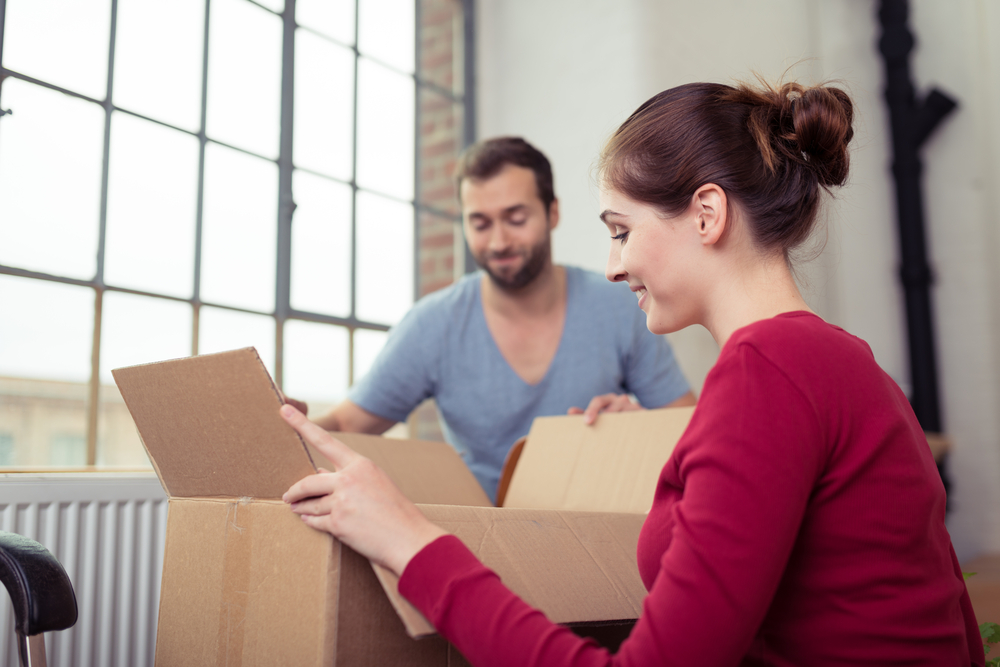
Britain faces the dual crises of a serious housing shortage and a construction industry that's losing skilled workers faster than it recruits them. Offsite construction...
The British construction industry has been slow to adopt offsite techniques in spite of the savings in time and money they offer to developers when compared to traditional onsite techniques. Also, offsite techniques tend to cause less environmental damage and local disruption. Here we discuss their financial and efficiency advantages.
This post is part of our series on offsite construction techniques. The others are:
Modern offsite construction techniques: an overview
Constraints to offsite construction in Britain
Can offsite construction solve Britain's housing crisis?
When it comes to offsite construction, Britain is a 'laggard country'. That's the conclusion of Dale Steinhardt and Karen Manley of the Queensland University of technology, who compared offsite construction [PDF] between several high-income countries. Less than 5% of construction in Britain uses offsite techniques, compared to around 9% in Germany, 12-15% in Japan and 20% in Sweden.
Yet Britain has the largest factory devoted to modular construction in the world, owned by Legal and General and sited in Sherburn, Yorkshire. They claim it has the capacity to build 3,000 new homes per year, showing Offsite construction is not an alien concept to the British construction industry.
The advantages of using offsite construction were laid out in a 2013 report [PDF] commissioned by Buildoffsite, a business organisation that aims to catalyse the use of offsite methods in the British construction industry.
A major theme of the report is that because offsite construction moves much of the building process from the building site into a factory, processes and conditions are more like the manufacturing industry than the traditional construction industry. It's a difference that underlies many of the advantages of offsite over onsite construction.
Want a more detailed look at how you can implement energy efficiency best practice?
Prefabricating the components of a building in a factory can be automated far more than the traditional onsite brick-by-brick approach. In particular, the construction of kitchen and bathroom pods in a factory allows the rooms with the most complex mechanical and engineering components to be prefabricated and transported to the site without needing to co-ordinate workers with the various skills, often working for different sub-contractors, who are needed to construct kitchens and bathrooms onsite.
Automation raises the frightening prospect of machines replacing human labour, stealing our jobs and leaving us unemployed and destitute. However, the prospect looks a lot less frightening in the context of a construction industry facing a severe labour shortage. The 2016 Farmer Review [PDF], published by the Construction Leadership Council, showed that four workers leave the construction industry for every one recruited into it. The loss of skilled workers is likely to get worse because nearly one in three construction workers are aged over 50 and will retire in the next 15 years. The industry is going to have to make do with a lot less workers in the coming years, so automation offers a way to fill the gap left by retiring humans.
The Farmer report describes a number of training and recruitment initiatives which will alleviate the problem but the numbers dictate that for the construction industry to continue to function as it is - which means only falling short of the government's target for home building by around 50% - the industry needs to either increase recruitment by more than five times or embrace less labour intensive techniques such as offsite construction.
It's instructive to consider the Lessons from Japan [PDF] described by William Johnson of the Bartlett School of Planning. Japan faced a worse construction skills shortage than Britain, exacerbated by an older population with a lot of people retiring and poor recruitment into construction, a very restrictive visa system that prevented recruitment of migrant labour and a 'scrap and rebuild spiral' that sees houses demolished and replaced at around eight times the UK rate. The Japanese embrace of offsite construction is key to Japan's annual offsite home production alone being around three-quarters of the UK's entire home production.
While the UK now a housing shortage, Japan now has a housing surplus.
Many older tower blocks supplied services like hot water and ventilation using central plants connected to each flat with a network of pipes and ducts, which need large rooms or basements to accommodate the plants. The pipes and ducts take up communal spaces like corridors, all of which must be accessible when it's time to hunt down a leak or check that the lagging is still insulating them properly.
Modern buildings may replace such centralised systems with more localised systems. For example, ventilation is handled by demand controlled ventilation systems in each flat rather than centralised plants, while the better insulation of modern buildings enables central heating systems to be replaced with electric convection and infra-red heaters in each room.
Such localised systems need to be installed by workers with specialist skills and each of them needs a particular set of materials, which is logistically much simpler - and therefore cheaper - to handle in a factory than to try to co-ordinate onsite.
Incorporating the building services into volumetric units enables them to be designed with a small number of electrical and plumbing connections that can simply be plugged in when the building is assembled.
Moving much of the construction from the site to the factory means a development spends less time actually at the construction site. Exactly how much less time depends on the nature of the construction project and how much of it is done offsite, but the Buildoffsite report says it can range from 25% in the case of large buildings like office blocks and supermarkets to 60% for simpler projects like schools.
Apart from cutting the costs of hiring generators and cranes, anyone who has ever had to prepare an environmental impact assessment will appreciate the opportunity to keep the local disturbance to a minimum. Some planning authorities give the impression that no building site should ever make noise or produce dust. While it will take more than offsite construction to make a planning authority happy, it can at least cut down the amount of onsite time that they'll need to approve.
Moving construction work from a site to a factory effectively means working in conditions equivalent to the manufacturing industry. Working indoors has to be better than on a building site during the next 'beast from the east', but the Buildoffsite report points out that there's an even stronger reason why offsite construction is better for the workers: they're less likely to die. While the construction industry's safety record has improved dramatically over the last three decades, the Health and Safety Executive reports [PDF] that the construction industry still has a fatal injury rate more than three times that of the manufacturing industry.
The construction industry's fatal injury rate of 1.64 per 100,000 workers per year is still very low: to have a 50/50 chance of a fatal injury, a worker would have to spend more than 30,000 years working in the industry - as long as modern safety standards are maintained until the year 32019. However, that still looks worse than the 95,000 years that worker would have to spend in the manufacturing industry to have the same risk.
More worrying is the effect that working in construction can have on a worker's health, particularly the various ailments that the Health and Safety Executive classes as musculoskeletal disorders: the various things that can go wrong with a worker’s back or limbs after years of heavy lifting even if he's never had an accident. With a rate of 2,310 per 100,000 workers per year, a worker only needs to spend 22 years in the industry to have a 50/50 chance of developing some sort of disorder. That's one of the highest musculoskeletal disorder rates of any industry and - what matters while we're talking about offsite construction - is that it's around twice the rate in the manufacturing industry.
Offsite construction would mean construction workers spending more time protected from the caprice of the British weather, with their feet on solid ground and with much of the heavy lifting done by machinery that's securely bolted to the floor.
As well as being safer, the better conditions may go some way to changing the perception of construction as an unpleasant sector to work in, as described in the Farmer report, and improve recruitment.
One thing any environmental impact assessment will look at is how many vehicles will be carrying workers and materials to the building site. The local residents are already sick of the school run traffic jam, and the last thing they want is a convoy of lorries adding to it. Nor do they want a procession of diesels spewing nitrates on their narrow road in the leafy suburbs.
Offsite construction can't do away with the need for vehicles altogether but reducing the time on site does mean the local residents won't have to put up with it for as long.
Perhaps more importantly, offsite construction tends to replace a lot of small vehicles with a few large ones. Unless the site is particularly difficult to access, a large vehicle doesn't contribute much more to a traffic jam than a small one and it generates a lot less noise and air pollution per tonne of load.
That one lorry carrying all the wall panels for the building is going to irritate the locals a lot less than a herd of vans carrying cement powder.
Since Part L of the building regulations came into force in 2010, new buildings have been required to adhere to strict standards of insulation. To meet those standards, the building design is subjected to the standard assessment procedure (SAP) to ensure that it does not leak too much heat, either through conduction through the building fabric or through air passing through the building. The building is assessed again once it's been built, including a physical pressure test to ensure that it is as close to airtight as it was designed to be.
The assessment's prediction of the building's energy performance can only be as good as the building's adherence to the design, and it's much easier to precisely meet design specifications in a factory than on a building site. That means that the design doesn't need to allow the margin for error necessary for onsite construction and once complete, it can be handed over to the owner with the full confidence that it need as little energy to keep it warm as the design says it will.
As well as issues around energy efficiency, the Buildoffsite report estimates that the cost of remedying construction defects typically adds around 2% to the construction costs, which could be the difference between winning and losing a tender. The equivalent figure for the manufacturing industry is close to zero, indicating that defects are simply much less likely in the factory than on the building site. Moving construction offsite cuts the cost associated with remedying them.
The latest government statistics [PDF] show that the construction industry is responsible for more than half the total waste produced in the UK and although a lot of that is recycled, it still amounts to a large volume ending up in landfill. Perhaps more pertinent for the developer is that the Buildoffsite report estimates that dealing with construction waste amounts to 3-5% of the cost of a building project, which is substantially higher than the 1-3% waste cost in manufacturing.
The difference is partly because the processes in a factory are much more predictable than on a building site, meaning that materials can be ordered to more precisely calculated requirements, and partly because it's easier and cheaper to handle waste in the factory setting.
As well as the solid waste that goes to landfill, the machinery used in construction can't avoid pumping various pollutants into the atmosphere. However, if air pollution can't be avoided, it can at least be minimised. We've already discussed how reducing works traffic reduces noxious nitrates, which limits local air pollution but greenhouse gases like carbon dioxide are a more global problem that are already causing significant climate change around the world. John Barrett and Thomas Wiedmann modelled the greenhouse gas emissions of an average new build house in the UK, using either offsite or onsite building techniques. They found that replacing onsite with offsite construction would cut the greenhouse gas emissions by anything from 17% to 30%.
Barrett and Wiedmann's model considered both the construction itself and the energy usage of the house when people are living in it. They found that the materials used in offsite manufacturing generated around half as much greenhouse gas emissions as onsite materials as well as making for a much more energy efficient fabric to the house.
In spite of all these advantages, Britain remains one of Steinhardt and Manley's laggards when it comes to the uptake of offsite construction, alongside the USA and Australia. The advantages are not the whole story.
The other side of the story is of the constraints to the wider uptake of offsite construction in Britain, which we discuss here.
If you'd like to ask us anything more about offsite construction, or how Atamate building intelligence can be integrated into an offsite project, please contact us now.
Britain faces the dual crises of a serious housing shortage and a construction industry that's losing skilled workers faster than it recruits them. Offsite construction...
A range of modern methods of construction (MMC) is revolutionising the construction industry. Many involve work being done in factories rather than building sites, hence...